Exploring Industrial Controls: Technologies, Benefits, and Implementation Strategies
Industrial controls are integral to the successful operation of manufacturing and production facilities worldwide. These control systems are responsible for automating and managing the machinery and equipment involved in industrial processes. They enable industries to monitor, control, and optimize production processes, ensuring efficiency, safety, and reliability. Industrial controls encompass a broad range of technologies, from simple switches to complex distributed control systems (DCS) and programmable logic controllers (PLC). This article delves into the different types of industrial control systems, their importance, the benefits they provide, and the challenges faced in implementing them. Through exploring the technological advancements and best practices in industrial controls, businesses can optimize their operations and gain a competitive edge in the marketplace.
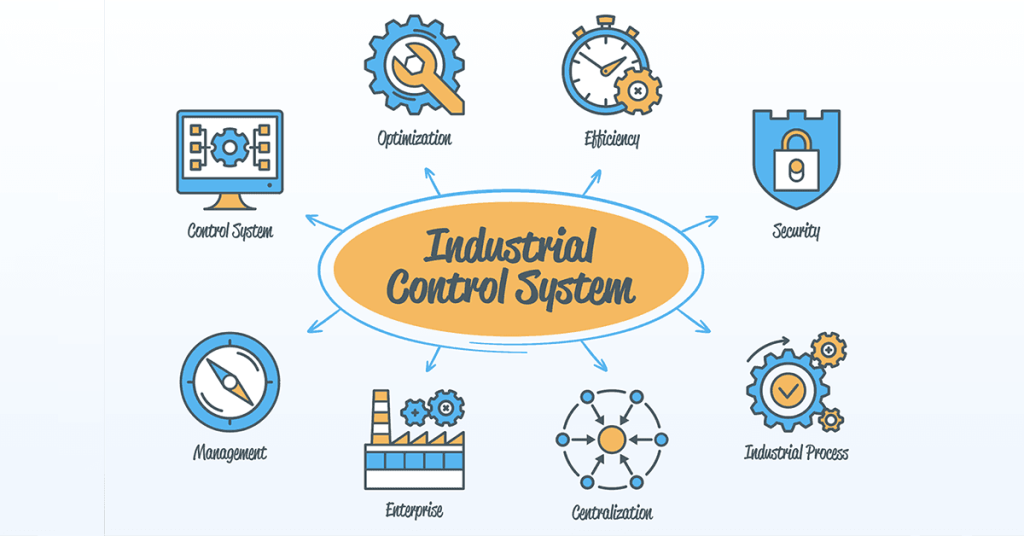
What Are Industrial Controls?
Industrial controls refer to the mechanisms used to monitor and manage industrial processes. These systems automate operations in industries like manufacturing, energy, water treatment, and transportation. Industrial controls are used to ensure that production processes run smoothly, safely, and efficiently by controlling machinery, processes, and workflows. Whether through basic equipment like switches or complex systems like SCADA (Supervisory Control and Data Acquisition), industrial controls are designed to maintain constant process regulation and allow real-time monitoring.
Industrial controls include hardware and software systems such as sensors, controllers, and actuators. These elements interact with each other to regulate and monitor various processes. By using industrial controls, businesses can improve productivity, reduce operational costs, and ensure product quality.
Types of Industrial Controls
There are several types of industrial controls, each designed to suit specific operational needs. The following are the most common types used in industrial settings:
1. Programmable Logic Controllers (PLC)
PLCs are highly versatile and reliable control systems used in industrial automation. They are programmable devices that control processes by receiving input from sensors, processing this data, and sending commands to actuators. PLCs are typically used in discrete manufacturing processes such as packaging, assembly, and material handling.
-
Advantages:
- Reliable and cost-effective
- Easy to program and modify for different tasks
- Can handle complex automation requirements
-
Applications:
- Automotive assembly lines
- Conveyor systems
- Food processing plants
2. Distributed Control Systems (DCS)
DCS is typically used in industries where continuous processes are required, such as in chemical, oil, gas, and power generation. These systems consist of a network of controllers distributed across different plant areas to control various processes simultaneously. Unlike PLCs, DCS systems handle analog data and control loops with precision, ensuring stability in complex and large-scale operations.
-
Advantages:
- High reliability and scalability
- Suitable for complex and continuous operations
- Advanced data analysis capabilities
-
Applications:
- Power plants
- Water treatment facilities
- Oil refineries
3. Supervisory Control and Data Acquisition (SCADA)
SCADA systems are used to monitor and control large-scale processes, often remotely. They provide a centralized platform where operators can view real-time data, control devices, and manage alarms. SCADA systems are used in critical infrastructure like energy grids, water systems, and industrial manufacturing facilities.
-
Advantages:
- Remote monitoring and control
- Ability to control large, geographically dispersed operations
- Real-time data collection for enhanced decision-making
-
Applications:
- Electrical grids
- Water distribution networks
- Oil and gas pipelines
4. Human-Machine Interface (HMI)
HMI is the user interface that allows operators to interact with industrial control systems. It displays real-time information, such as process parameters, system status, and alarms, allowing operators to monitor and adjust processes. Modern HMIs can be touchscreen-based and provide more intuitive control over industrial systems.
-
Advantages:
- Intuitive and user-friendly interface
- Real-time data visualization
- Easy identification of system faults and performance issues
-
Applications:
- Manufacturing floors
- Process control rooms
- Transportation systems
The Benefits of Industrial Controls
The implementation of industrial control systems can provide a wide range of benefits for businesses in various sectors. Below are some of the key advantages:
1. Enhanced Efficiency and Productivity
Industrial controls help automate processes, reducing the need for manual intervention and enabling continuous operation. By automating tasks such as assembly, packaging, and quality control, businesses can optimize workflows, reduce downtime, and increase production rates. Automation also ensures that processes are performed consistently, resulting in higher quality products.
2. Improved Safety
Safety is a major concern in industries dealing with hazardous materials or complex machinery. Industrial control systems can enhance safety by monitoring critical variables like temperature, pressure, and flow, providing alerts or shutting down operations if parameters exceed safe thresholds. These systems also minimize the risk of human error by automating routine tasks.
3. Cost Savings
Implementing industrial control systems can lead to significant cost savings. Automation reduces labor costs, increases operational efficiency, and minimizes energy consumption. Moreover, real-time monitoring helps identify inefficiencies and potential issues, allowing businesses to take corrective actions before they result in costly downtime or damage.
4. Real-time Monitoring and Data Analysis
Industrial control systems provide real-time monitoring of processes, offering valuable data for analysis. With the help of data analytics, businesses can optimize operations, predict maintenance needs, and improve decision-making. The data collected by control systems can also be used for regulatory compliance, providing a transparent record of operations.
5. Flexibility and Scalability
Industrial control systems are highly flexible and scalable, enabling businesses to adjust their operations according to changing needs. Whether scaling up production capacity or introducing new processes, control systems can be easily modified and expanded to accommodate these changes.
Challenges in Implementing Industrial Controls
While industrial control systems offer many benefits, there are several challenges businesses may face during implementation:
1. Integration with Existing Systems
Many businesses use legacy systems that may not easily integrate with new industrial control systems. The integration of these systems often requires substantial effort, time, and resources to ensure smooth communication between different devices and platforms.
2. Cybersecurity Risks
As industrial control systems become more connected to networks and the internet, the risk of cyberattacks increases. Protecting these systems from cyber threats such as hacking, malware, and ransomware is a critical concern. Implementing robust cybersecurity measures, such as firewalls, encryption, and regular system updates, is essential to safeguarding control systems.
3. Complexity of Maintenance and Upgrades
Maintaining industrial control systems can be complex and require specialized knowledge. Moreover, as technology evolves, older control systems may need to be upgraded or replaced to ensure continued efficiency and security. Balancing system upgrades with ongoing operations can be challenging, especially in industries with tight production schedules.